Uncovering Manufacturer Failures in Consumer Product Cases
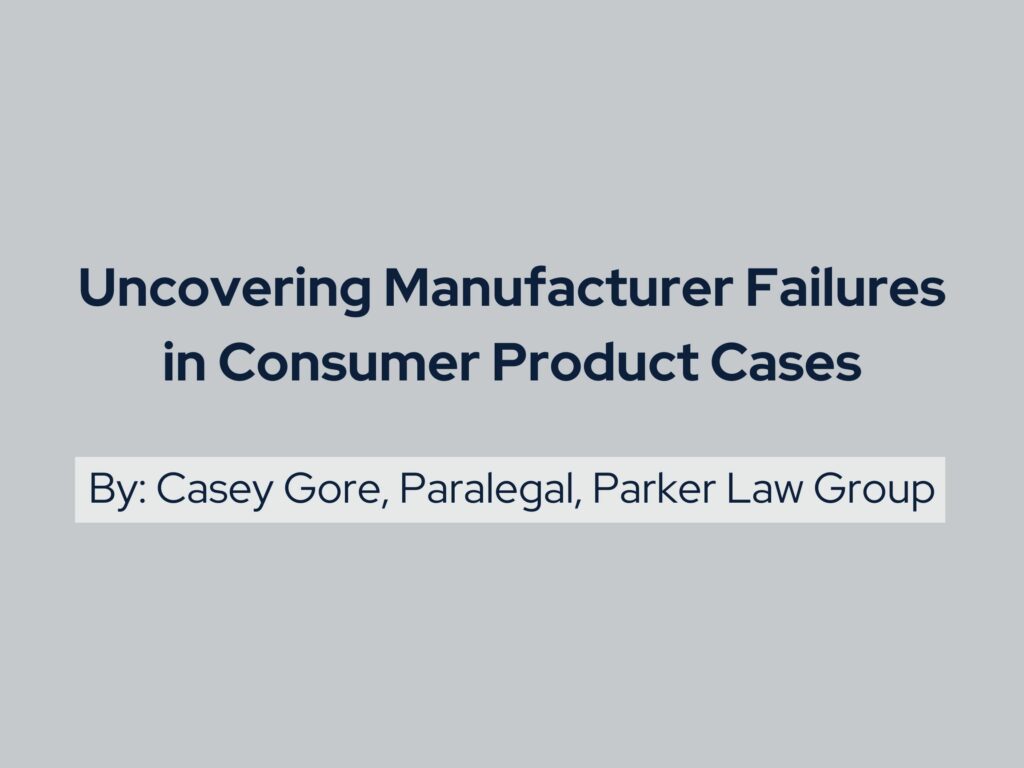
By: Casey Gore
Throughout the various stages of product development, any number of things can go wrong, leading to dangerous and defective products and ultimately resulting in those injured seeking recompense. That is where our firm comes in. In order to build the most effective case for each client, we must examine the supply chain and every company within it, analyzing their respective roles and ferreting out all the potential areas that could have contributed to any hazards and defects in the product in question. For the sake of simplicity, this article will focus on the manufacturer, the entity responsible for the design and production stages of product development.
The U.S. Consumer Product Safety Commission has developed the Handbook for Manufacturing Safer Consumer Products to guide manufacturers in designing and producing goods that prioritize consumer safety. This resource aims to provide best practices, safety principles, and regulatory insights to ensure that products meet the highest safety standards while minimizing risks to users. By referencing the guidelines in this handbook, law firms can uncover evidence of negligence or noncompliance in consumer product cases, strengthening their arguments for injured parties.
In the handbook, the U.S. Consumer Product Safety Commission states, “…safety must be designed into and built into consumer products in the United States…” U.S. Consumer Product Safety Commission. (2006). Handbook for Manufacturing Safer Consumer Products. Typically, when a defective product reaches our firms by way of an injured consumer, this simple principle was not adhered to, and we need to find the evidence to prove that. In order to do this, we must first understand the best practices of manufacturing. Once we know these, we are better equipped to pinpoint the areas of failure.
The main point of reference guiding this article is the Handbook for Manufacturing Safer Consumer Products published in 2006 by the U.S. Consumer Product Safety Commission. While most of the practices outlined in this handbook are voluntary and not legal requirements, they are industry best practices and provide a valuable and authoritative frame of reference by which to critique manufacturers. These best practices can be condensed and divided among four areas of manufacturing: (1) Management Level, (2) Design Stage, (3) Production Stage, and (4) Post-Production. Below, I will provide a brief, but not exhaustive, summary of the tenets of these core areas.
- Management Level
Safety should be a core value of the culture and management of the manufacturing company. A manufacturer should develop and mandate a formal product safety policy endorsed by top management and publicized widely within the organization (Handbook, p. 8). Additionally, safety should be prioritized alongside other business goals like profitability and efficiency, so a dedicated safety team or personnel should be established, and their safety responsibilities should be clearly outlined (p. 8).
Ensuring that each employee is properly and regularly trained for their respective roles is crucial to this culture of safety. The training should be applicable to the individual or team to which the training is provided (p. 9). For example, the training provided to senior executives may cover, among other things, how to implement a product safety process, while the training for product designers and engineers should focus on, among other skills, foreseeable use analysis, test methods, and safety standards (p. 9). Furthermore, each employee should have the requisite skills needed to do their specific job effectively. For instance, if an individual is designing a product, they should have the specialized knowledge required to safely and capably design that specific product (p. 20).
- Design Stage
In order for safety to be built into the design of a product, the designers or design team should perform comprehensive design reviews. The goal of these design reviews is to timely identify potential product hazards through the meticulous examination of all aspects of the product, including the materials, each component part and the configuration of these component parts, packaging, and labeling (p. 9). Design reviews are conducted by way of Foreseeable Use Analyses which are reviewed by a multi-faceted review team (pp. 9, 10).
A foreseeable use analysis takes into account how a consumer might use and/or interact with a product and is a critical step in the design process (p. 9). “Foreseeable use” refers to both the manufacturers intended use as well as the unintended uses that can reasonably be anticipated (p. 9). One type of foreseeable use analysis is a Failure Modes Effects Analysis (FMEA) (p. 9). During an FMEA, each component part is examined in an effort to determine how it might fail and what the consequences of said failure would be (p. 10). A fault tree analysis is essentially the reverse of an FMEA in that it works backwards from the consequence to uncover the sequence of events that lead to that consequence (p. 10). If and when safety hazards are identified, corrective action must be taken to design out these hazards whenever possible (p. 10). If it is not possible to design out these hazards, warnings should be designed and implemented to adequately warn the consumer of the hazard.
The team reviewing the risk analyses should consist of members who are knowledgeable about various aspects of safety and manufacture, such as consumer services, quality assurance, and standards and regulations (p. 10). If a company does not have the adequate expertise to perform these reviews in-house, they should look into outsourcing them (p. 10).
- Production Stage
There are a lot of considerations and safety measures to be taken during the production stage. The safety of products depends on the quality of the raw materials and the assembly process (p. 10). Manufacturers should maintain strict control over suppliers through clear and precise purchase documents outlining design and safety requirements and, additionally, through inspections and audits of the suppliers’ facilities, operations, and materials, ensuring these materials meet their design specifications and industry standards (pp. 10, 11).
Many manufacturers outsource production to overseas factories. As such, it is crucial for manufacturers to provide detailed work instructions to these factories (p. 11). Among many other things, these instructions should convey how to perform inspections and testing to ensure the manufactured products meet design specifications and industry standards and should also include a means to keep track of the data from these tests (p. 11). Manufacturers should make sure their factories keep detailed records of not just testing data, but also records of specific operations within the factory and the identity of individuals performing these operations and their training and qualifications (p. 11).
Quality control processes should be established within factories. Prior to distribution, consumer products must be inspected and tested (p. 12). Testing and inspections should continue throughout production, with some products requiring the testing and inspection of each unit while others may be tested via a sample of products in a manner that is standardized and conforms to regulations (p. 12). Manufacturers should visit their factories periodically to confirm that all stages of production are in compliance with their design specifications and industry standards. They should also make sure measures are in place to overcome any potential language barriers that may exist.
- Post-Production
Safety does not end with production. Manufacturers should ensure they have an effective product safety system in place to monitor their products post-sale, so detailed record keeping is paramount (p. 13). A system should be in place to handle consumer complaints and commentary and to document any actions taken in response (p. 13). Should corrective action need to be taken to change a design or some aspect of production, these changes should be made a matter of record and there should be a system in place to make sure these changes are incorporated into all documentation affecting the product (p.10) In the event a recall is needed, it is vital the manufacturer is able to locate products within the production and distribution system so appropriate actions can be taken and a prompt and successful recall can be achieved (p. 13).
Under the Consumer Product Safety Act (CPSA), a manufacturer is required to report certain things to CPSC. Among these, under Section 15 (b) of the CPSA, they are required to report information which reasonably supports the conclusion that a product does not comply with a safety rule issued under the CPSA, or contains a defect which could create a substantial risk of injury to the public or presents an unreasonable risk of serious injury or death, within 24 hours of obtaining this information, 15 U.S.C. § 2064(b). Manufacturers are also required to report information about settled lawsuits to CPSC under Section 37 (b) of the CPSA, 15 U.S.C. § 2084.
In conclusion, the Handbook for Manufacturing Safer Consumer Products serves as a vital reference for evaluating and critiquing manufacturers’ practices. Although its recommendations are largely voluntary, they represent industry best practices across all phases of manufacturing. By adhering to these principles, manufacturers can enhance product safety and reduce consumer risk. Understanding and applying the insights from this handbook not only benefits manufacturers but also equips representatives with a robust framework to ensure accountability to safety standards in the marketplace.
Reference:
U.S. Consumer Product Safety Commission. (2006). Handbook for Manufacturing Safer Consumer Products. https://www.cpsc.gov/s3fs-public/pdfs/blk_pdf_handbookenglishaug05.pdf